2025 Forfatter: Howard Calhoun | [email protected]. Sist endret: 2025-06-01 07:14
Bruk av investeringsmodeller er en ganske populær metode for støperiproduksjon. Metoden utmerker seg ved kompleksiteten til den teknologiske prosessen og høye arbeidskostnader for forberedende prosesser. Derfor brukes den der det er nødvendig å observere dimensjonene nøyaktig og sikre høy kvalitet på overflaten til delene. Slik støpes turbinblader og høyytelsesverktøy, proteser og smykker, samt skulpturer med kompleks konfigurasjon. Essensen av tapt voksstøping er at formen for støping er i ett stykke, modellen med lavtsmeltende materialer fjernes ikke under støping, men smeltes. Dette sikrer nøye overholdelse av dimensjoner og relieff. Metall helles inn i hulrommet som er igjen fra modellen. Etter fullført avkjøling blir formen ødelagt og produktet fjernet. Ved støping av store serier reduseres kostnaden for produktet.
metodefordeler
Den største fordelen med investeringsstøping er nøyaktigheten av muggoverføring og lav overflateruhet. I tillegg er andre fordeler tilgjengelige:
- Produksjon av lett bearbeidede legeringsdeler tilgjengelig.
- Reduserer behovet for ytterligere maskinering.
- Produkter støpes som ellers måtte lages i deler og settes sammen.
- Med store serier oppnås en reduksjon i spesifikk arbeidsintensitet (per ett produkt) og kostnadene.
- Mulighet for mekanisering og delvis automatisering av de forberedende operasjonene av selve støpingen.
Disse fordelene gjør metoden til en av de mest populære og brukt i dagens metallurgi, spesielt i kombinasjon med moderne progressive støpemetoder.
Ulemper med investeringscasting
De utvilsomme fordelene med metoden, ser det ut til, burde ha sikret dens dominans blant andre metoder. Til tross for populariteten til investeringsstøpemetoden, har imidlertid ulemper forhindret dens utbredte bruk. Den største ulempen er kompleksiteten til flertrinnsprosessen. Det krever ganske komplekst og dyrt teknologisk utstyr for de forberedende stadiene. For enkle produkter produsert i små partier har denne metoden en høyere kostnad.
For kostnadseffektiv anvendelse av investeringsstøping sammenlignes fordeler og ulemper ved metoden, beslutningen omvalget er tatt på grunnlag av en vurdering av forholdet pris/kvalitet. Derfor brukes den hovedsakelig til de mest kritiske og kostbare produktene som er vanskelige å få tak i på noen annen måte, som turbinblader, skulpturer, høyhastighetsverktøy osv. Et annet bruksområde er storskala støpegods, i som skalaeffekten gjør det mulig å oppnå en betydelig kostnadsreduksjon
Teknologi
Investeringsstøpeteknologi er en flertrinns produksjonsprosess som er relativt arbeidskrevende. På det første trinnet lages en mastermodell, den vil bli standarden for produksjon av arbeidsmodeller etter å ha gått gjennom alle stadier av sluttproduktet. For produksjon av en mastermodell brukes både spesielle modellkomposisjoner og tradisjonelle - gips eller tre. Materialet til mastermodellen skal kombinere styrke og enkel behandling.
Ytterligere sørger investeringsstøpeteknologi for å lage en form som alle arbeidsmodeller skal støpes inn i. Former er laget av gips, gummi, silikon, sjeldnere metall. Strukturelt må den nødvendigvis være avtakbar og utformet for gjentatt bruk. Formen fylles med en modellsammensetning, etter at den har stivnet, demonteres den og neste arbeidsmodell fjernes.
Når du produserer unike deler eller små opplag, hoppes trinnene med å lage en masterlayout og en form over, og en layout (eller flere) lages ved å støpe materialet manuelt.
Neste trinn i investeringsstøpeprosessen erproduksjon rundt oppsettet (eller blokken med oppsett) av støpeformen. Disse matrisene er strukturelt allerede ikke-separerbare og disponible, noe som gjør det mulig å oppnå nøye overholdelse av dimensjonene og ruheten til produktet. I moderne industri brukes to typer støpeformer - tradisjonelle sandleireformer for støping i bakken og skallformer - for produksjon av presise og kostbare deler.
Etter at formen er ferdig, smeltes modellen fra den ved oppvarming eller blåsing med overopphetet damp. Skallformene forsterkes i tillegg ved å varme opp til 1000 ˚С.
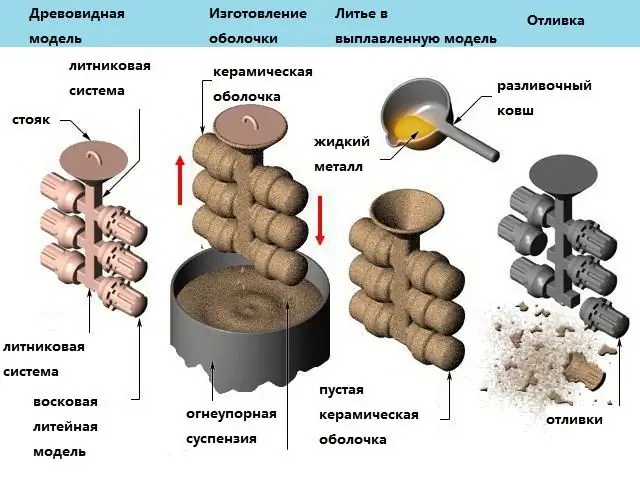
Det siste stadiet av prosessen inkluderer selve støpingen av produktet, avkjøling under naturlige forhold eller ved en spesiell metode i en termostat, destruksjon av mugg og rengjøring av produktet. Metoden gjør det mulig å oppnå støpegods av høy kvalitet som veier fra flere gram til titalls kilo.
modelloppstillinger
Materialet for produksjon av layout må ha visse egenskaper. Den bør ha egenskaper som:
- Plastisitet i fast fase. Det er nødvendig å gjenta formen på det fremtidige produktet nøyaktig og korrigere den om nødvendig.
- Styrke. Modellen må uten deformasjon tåle prosessen med å danne en form rundt den.
- Fusible. Å gjengi en modell bør ikke kreve mye tid og energi.
- Smeltet flyt. Komposisjonen bør lett trenge inn i alle fordypningene og detaljene i relieffet, og gjenta nøyaktig konturene av den fremtidige detaljen.
- Økonomi. Spesielt viktig for stor serieproduksjon.
For modellsammensetninger brukes vanligvis en blanding av stearin og parafin. Disse materialene utfyller hverandres parametere på en vellykket måte, og kompenserer for det utilstrekkelige smeltepunktet til parafin og den for høye viskositeten til stearin.
Komposisjoner basert på brunkull er ikke mindre populære i bransjen. Hovedegenskapene er fuktmotstand, styrke og evnen til å danne svært glatte belegg, noe som er spesielt verdifullt for produktmodellering.
Forbindelser som består av en blanding av brunkullvoks, parafin og stearin brukes også.
Muggfremstilling
For produksjon av unike produkter utarbeides en layout ved å kutte ut et stykke modellmateriale manuelt eller etter maler. Modeller i form av revolusjonskropper er også laget på dreiebenker. I det siste har metoden for 3D-printing av modeller blitt mer og mer utbredt. Den passer for både enkeltoppsett og små serier.
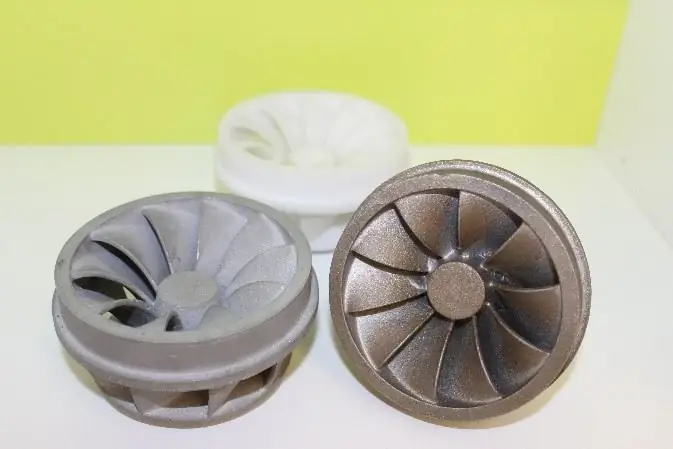
Kostnadene for en moderne industriell 3D-skriver er fortsatt høy, men på grunn av den enkle rekonfigureringen fra ett produkt til et annet, kan det bli et effektivt modellverktøy i tilfelle et stort antall heterogene småseriebestillinger.
For å lage et stort antall identiske layouter, lages en matrise av gips, gummi, silikon eller metall. Arbeidsoppsett produseres i sin tur ved å støpe inn i en matrise. Formen skal etter design være sammenleggbar for å sikre muligheten for å produsere et gitt antall modeller. Det valgte materialet bør også gi en slik mulighet, derfor stilles det slike krav til det som styrke, tetthet, lav ruhet og kjemisk treghet i forhold til utformingen. Formstoffet må også ha minimal vedheft til mock-upen for å sikre at de ferdige mock-upene enkelt kan fjernes og dimensjoner overholdes. En viktig egenskap ved formen er dens styrke og slitestyrke, spesielt for store serier.
Å lage modeller og blokker
En mye brukt metode for å produsere investeringsmodeller er å støpe dem under lavt trykk i former. Injeksjonen av væskeblandingen utføres både manuelt, ved bruk av stempelsprøyter, og mekaniske, hydrauliske eller pneumatiske superladere. Ved bruk av brunkullvoks er det nødvendig å varme opp rørledningene for tilførsel av sammensetningen på grunn av dens høye viskositet. Modeller av ekspandert polystyren er laget ved ekstrudering på automatiserte støpemaskiner.
For å øke den økonomiske effektiviteten og redusere arbeidsintensiteten ved serieproduksjon av små støpegods, er layoutene deres kombinert i blokker. Portsystemer dannes over blokkene ved å feste individuelle oppsett til innløpene ved hjelp av et håndloddejern. Ved enkeltstøpte eller små serier lages modellene for hånd.
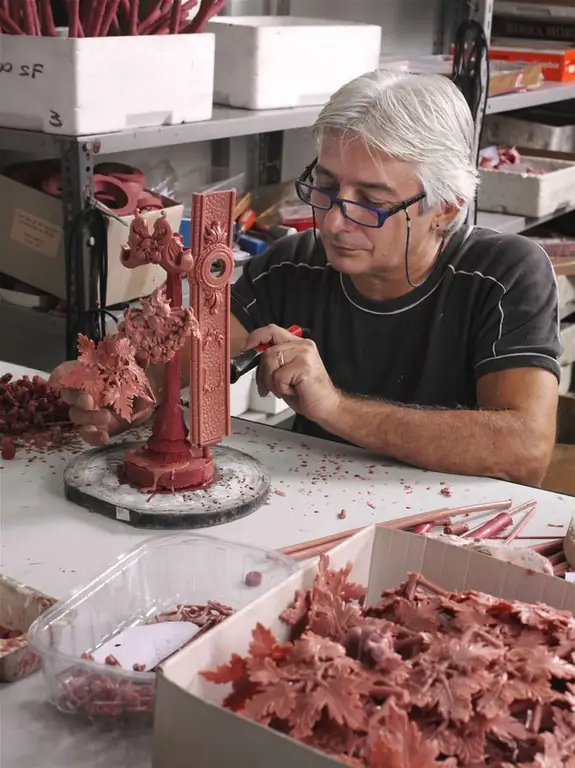
Ved forming av portsystemer er det nødvendig å sikre ikke-turbulent flyt av smelten, jevn fylling av alle elementer i matrisen. Når du fyller ut et skjema fra PGS, må du også overvåke enhetlig utfylling av alleåpninger mellom innløp og hindre skade.
Lage en form
I investeringsstøpemetoden som vurderes, er det to hovedtyper av former:
- Sand-leireblandinger (SGM).
- Shell.
Voksstøpeformer med flued brukes hovedsakelig i produksjon av små serier med produkter som ikke krever særlig høy nøyaktighet. Prosessen med produksjonen deres er ganske arbeidskrevende og krever høye og ofte unike ferdigheter fra modellbyggere og støpere. Delvis mekanisering egner seg bare til visse operasjoner, for eksempel klargjøring og fylling av støpesanden, stamping av den.
Skallformer, derimot, brukes til å produsere deler som krever spesiell produksjonspresisjon. Produksjonsprosessen er mer kompleks og langvarig, men den egner seg bedre til mekanisering.
Ground casting
Dette er den tidligste metoden for metallbearbeiding som er mestret av menneskeheten. Det ble mestret av våre forfedre samtidig med begynnelsen av bruken av metallprodukter som våpen, verktøy eller redskaper, det vil si for rundt 5 tusen år siden. Smeltet metall helles i en forberedt matrise fra en blanding av sand og leire. De tidligste stedene for metallbearbeiding oppsto nettopp der forekomster av metaller i form av nuggets og placers var lokalisert i nærheten. Et typisk eksempel er Kasli-anlegget i Ural, verdenskjent for sin blondestøping av jern.
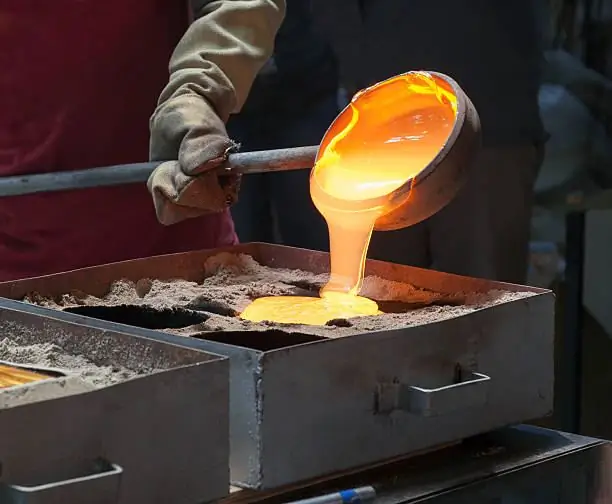
Investeringsstøpemetoden brukes til fremstilling av metallprodukter - både jernholdige ogfarget. Og bare for metaller som viser økt tendens til å reagere i væskefasen (som titan), er det nødvendig å lage matriser fra andre sammensetninger.
Produksjonsprosessen for støping i PGS består av følgende faser:
- modellfremstilling;
- forbereder kolben;
- fylling og komprimering av blandingen i kolben;
- metallstøping;
- fjerning og rengjøring av støpegodset.
Skjema fra ASG - engangsbruk. For å få det ferdige produktet, må det brytes. Samtidig er det meste av blandingen tilgjengelig for gjenbruk.
Komposisjoner av overveiende kvartssand av ulike kornstørrelser og plastleire, hvor innholdet varierer fra 3 til 45 prosent, brukes som materialer for ASG. Så for eksempel produseres kunststøpegods med en blanding med 10-20 % leireinnhold, for spesielt store støpegods justeres leireinnholdet til 25 %.
To undertyper brukes:
- Facingblandinger. De er plassert på den indre overflaten av formen og samhandler med det smeltede metallet. De må være varmebestandige, i stand til å ikke ødelegges av temperaturforskjeller og de resulterende spenningene. Disse blandingene har et fint korn for nøye å formidle detaljene til overflaten. Blandingens evne til å passere gass er også svært betydelig.
- Fyllblandinger. De brukes til tilbakefylling mellom dekklaget og veggene i kolben. De må tåle vekten av det hellede metallet, beholde formen på produktet og bidra til rettidig og fullstendig fjerning av gasser. Produsert av billigere sandkvaliteter,gjenbrukbar.
Hvis støpegassene ikke slipper ut gjennom massene av støpesand, men gjennom portsystemet, oppstår defekter i støpingen som fører til ekteskap.
Den tradisjonelle teknologien for støping i bakken er illustrert i detalj i A. Tarkovskys film "Andrei Rublev". I novellen "Klokken" leder den unge mannen Boriska, sønn av en avdød mester, en støperiartell og støper en kirkeklokke.
Shell-casting
Metoden for investeringsstøping i skallformer kjennetegnes av den beste overføringen av produktdimensjoner og lav overflateruhet. Modellen er laget av smeltbare forbindelser, som brunkullvoks. Støperier bruker også mye sammensetningen av parafin-stearin i like proporsjoner. Ved støpegods av store størrelser er s alter inkludert i modellmaterialet for å beskytte modellen mot deformasjon. Ved å dyppe ned i løsningen dekkes modellen i 6-10 lag med en høytemperatursuspensjon.
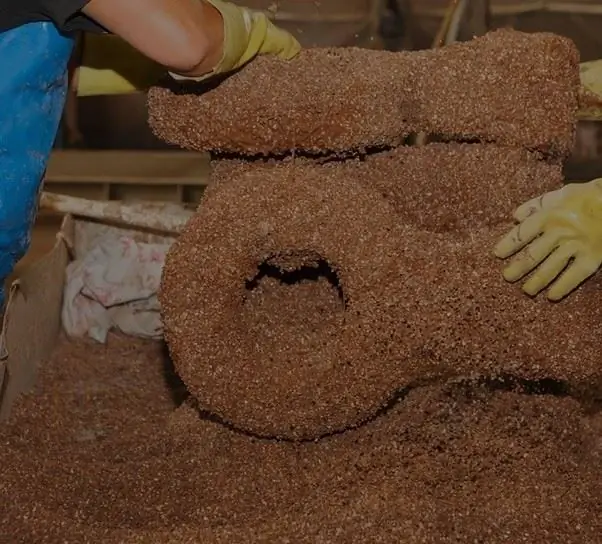
Hydrolyserte silikater fungerer som et bindemiddel, elektrokorund eller kvartskrystaller tas som varmebestandig sprinkling. Skallformmaterialer er preget av høy styrke, lav hygroskopisitet og utmerket gasspermeabilitet.
Layouten er tørket i en atmosfære av gassformig ammoniakk. På neste trinn varmes formen opp til 120 ˚C for å fjerne parafinmodellen. Restene av blandingen fjernes med overopphetet damp under høyt trykk. Deretter kalsineres formen ved temperaturer opp til 1000 ˚С, noe som fører til endelig fiksering og fjerning av stoffer,som kan frigjøres som gasser under støpeprosessen.
Skallet legges i en slags kolbe, som er dekket med stålhagl. Dette bidrar til å opprettholde konfigurasjonen når du fyller formen med smelte og forbedrer samtidig betingelsene for avkjøling av støpegodset. Smelten helles i former oppvarmet til 1000 ˚С. Etter avkjøling av produktet i henhold til et spesialprogram i termostat, ødelegges formen, støpegodset fjernes og rengjøres.
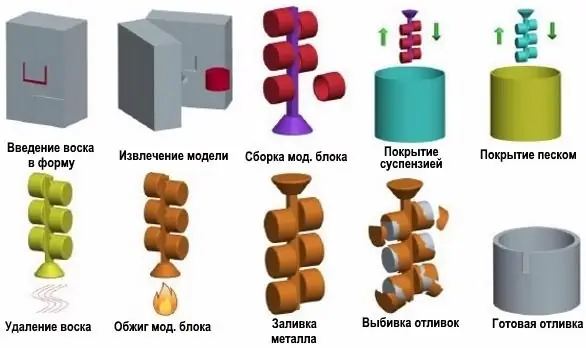
Den største fordelen med denne støpemetoden er høy dimensjonsnøyaktighet og lav overflateruhet.
Ytterligere fordeler med metoden:
- Støpe deler av legeringer som er vanskelige å bearbeide.
- Støpe gjenstander som ellers måtte støpes stykkevis og deretter settes sammen igjen.
Ulempene med denne investeringsstøpemetoden er lav metallutnyttelse og økt arbeidsintensitet.
Presisjonsstøping
Presisjonsinvesteringsstøping - dette er navnet på både teknologien og selve sluttproduktet. Den høye nøyaktigheten av støpingen er sikret av det faktum at under forberedelsen av formen er det ikke nødvendig å trekke ut modellen av produktet fra den. Ved bruk av den tradisjonelle metoden er produksjonen av en støpematrise en kompleks og svært tidkrevende flertrinnsprosess. Dette gjelder spesielt når det gjelder støping av deler med kompleks konfigurasjon, med utsparinger, fordypninger og indre hulrom.
Når du for eksempel støper en vase av støpejern eller kobber med variabel overflatekrumning, må du bruke mange triks. Ja, førstden nedre halvdelen av kolben er fylt, deretter fjernes modellen, snus og den øvre halvdelen rammes. Modellen må lages sammensatt, håndtakene på vasen er laget av to elementer, de trekkes ut gjennom modellhulen i to trinn - først det nedre elementet, deretter det øvre. Alle disse tallrike vendingene og slepingen kan ikke ha en positiv effekt på integriteten til formoverflaten og til slutt på nøyaktigheten av å opprettholde dimensjonene til støpingen og kvaliteten på overflaten. I tillegg gjenstår problemet med å nøyaktig matche delene av kolbene og feste dem sikkert til hverandre.
Produksjon av investeringsstøping er blottet for disse manglene, den krever ikke så høyt kvalifiserte modellbyggere og reduserer arbeidsintensiteten til pre-casting operasjoner betydelig. Dette er spesielt utt alt med store opplag med støpegods.
Metoden gjør det mulig å nå 2-5. nøyaktighetsklassen i henhold til GOST 26645-85. Dette gjør det mulig å støpe høypresisjonsprodukter som turbinblader, skjærende verktøy, inkludert høyytelses freser og bor, kritiske høybelastede braketter, små høyt belastede deler av kjøretøy, maskinverktøy og andre komplekse mekanismer.
Høy dimensjonsnøyaktighet og høy overflateklasse minimerer behovet for ytterligere maskinering av støpegodset, noe som sparer metall og reduserer produksjonskostnadene.
Utstyr
Investeringsutstyret for støpegods er variert og komplekst. Bedrifter kombinerer dem til et enkelt og godt koordinert kompleks,organisert som et sted, verksted eller separat produksjon.
Kompleksets sammensetning avhenger av produksjonsskala, størrelse, konfigurasjon og sirkulasjon av støpegods.
I produksjonen av proteser og smykker vil utstyret derfor inkludere:
- modellbord;
- dempeovn med termostat;
- et sett med skalpeller og spatler for å korrigere formen på modellen;
- forming board;
- flask;
- tanker for lagring og klargjøring av støpesand;
- sett med sandstamperverktøy;
- digel for smelting av metall;
- tang;
- hammer for å bryte formen.
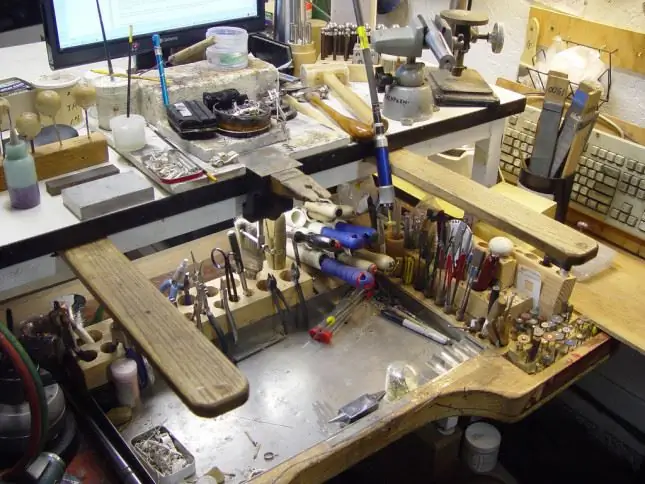
Dette produksjonskomplekset kan enkelt passe på ett bord og i ett skap. Hvis det er planlagt å masseprodusere for eksempel aluminiumsstøpegods - deler av en enhet, vil det kreves utstyr for:
- forme og helle keramiske former;
- tørkeformer;
- smelte ut modellmaterialet og påføre et varmebestandig lag;
- rengjøring av støpegods fra støpegods.
Og til slutt, selve utstyret til støperikomplekset, designet for å oppnå en smelte og helle den i en form. Det kan være støpeutstyr:
- under lavtrykk;
- sentrifugal;
- på vanlig gravitasjonsmåte.
Injeksjonsstøping og sentrifugalstøpemaskiner er en separat høymekanisert og automatisertproduksjonskompleks, isolert fra atmosfæren i butikken. De minimerer manuelt arbeid og menneskelig eksponering for skadelige forhold. Forseglede kamre som kompleksene er plassert i gir fullstendig fangst og rensing av eksosgasser, noe som øker bedriftens miljøvennlighet betydelig.
Støping av tapt voks har et ganske høyt potensial for utvikling, spesielt når det kombineres med avanserte støpe- og støpeteknikker.
Anbefalt:
Welsumer kyllingrase: beskrivelse, innhold, fordeler og ulemper, anmeldelser
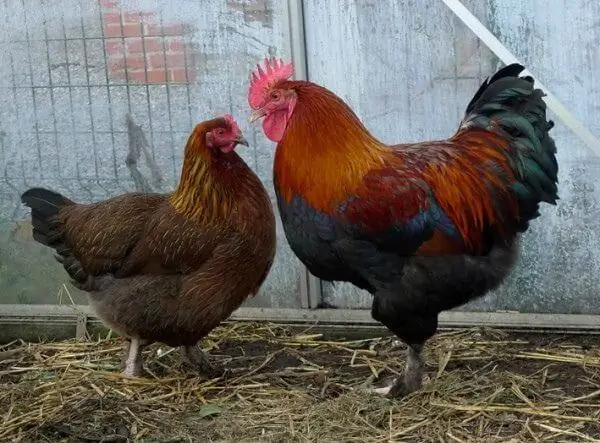
For personlige husholdningsplasser er ikke alltid kyllingrasen valgt ut fra produktivitet, for noen er utseende viktig. Det er vakkert når fugler med lys fjærdrakt går rundt i gården, som ikke trenger spesiell omsorg. Enda bedre når ekstern skjønnhet kombineres med utmerket ytelse. Disse kravene oppfylles av Welzumer-hønsrasen. Hun har mange positive egenskaper, derfor dyrkes hun ofte i private bakgårder
Investering i aksjefond: lønnsomhet, fordeler og ulemper. Regler for aksjefond
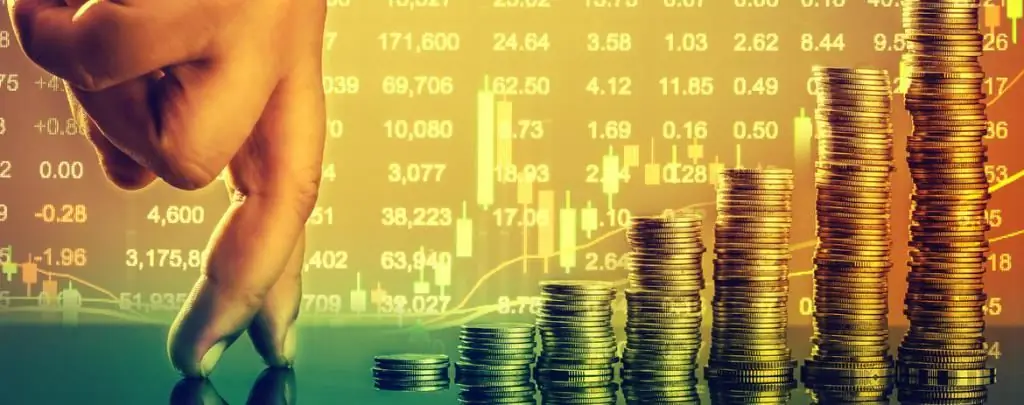
Et så interessant finansielt instrument som et aksjefond (aka aksjefond) dukket opp relativt nylig på territoriet til det tidligere Sovjetunionen. Og, det skal bemerkes, blant den generelle befolkningen om dem er ikke veldig godt kjent. Derfor vil det, innenfor rammen av artikkelen, søkes etter svaret på ett spørsmål: hva er aksjefond?
Pleksiglassgravering: fordeler og ulemper, teknologi, utstyr
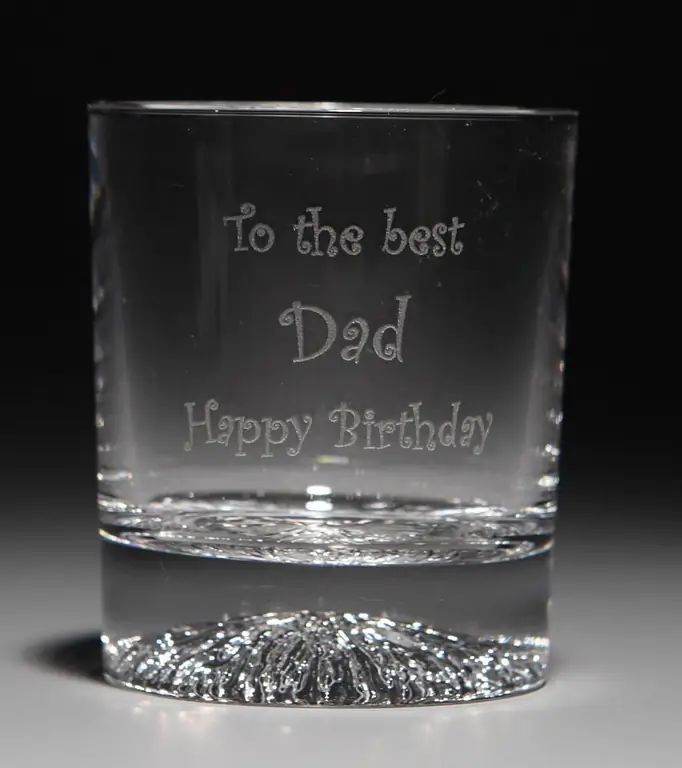
Pleksiglassgravering regnes som et malerhåndverk. En suvenirfigur, glassmalerier eller et glassbord, som er dekorert med utsøkte tegninger, legemliggjør en delikat kunstnerisk smak. Beising og sandblåsing teknologier er i fortiden. I dag, ved hjelp av en lasermaskin, kan hver person lage et svært detaljert mønster
Ultralydbehandling: teknologi, fordeler og ulemper
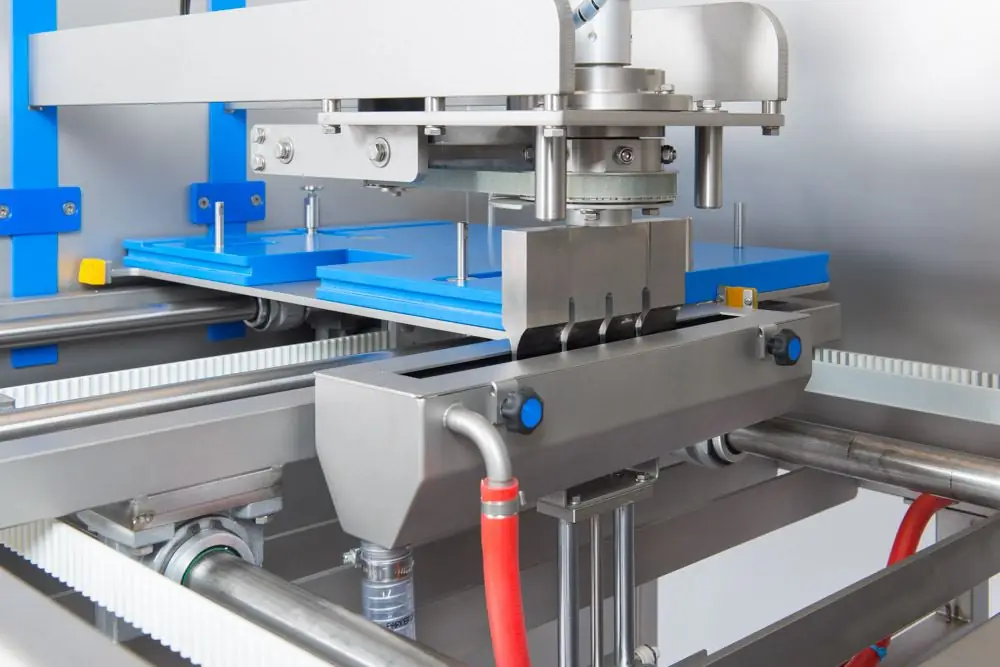
Metallbearbeidingsindustrien på dette stadiet av utviklingen er i stand til å løse de komplekse oppgavene med å kutte og bore arbeidsstykker med ulik hardhetsgrad. Dette ble mulig på grunn av utviklingen av fundament alt nye måter å påvirke materialet på, inkludert en bred gruppe elektromekaniske metoder. En av de mest effektive teknologiene av denne typen er ultralydbehandling (UZO), basert på prinsippene for elektroakustisk stråling
Kammertørking av tre: teknologi, fordeler og ulemper
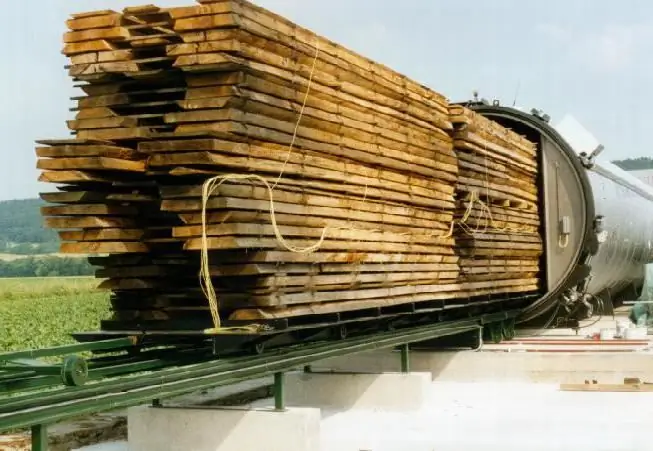
Artikkelen er viet kammertørking av tre. Tørketeknologien, stadier og hovedoperasjoner, samt dens fordeler og ulemper vurderes