2025 Forfatter: Howard Calhoun | [email protected]. Sist endret: 2025-06-01 07:14
Lederen for enhver bedrift, uansett aktivitetsfelt, drømmer om at fortjenesten vokser og produksjonskostnadene forblir uendret. "5S"-systemet i produksjon (i den engelske versjonen 5S), som kun er basert på rasjonell bruk av interne reserver, bidrar til å oppnå dette resultatet.
Dette systemet ble ikke opprettet fra bunnen av. Noe lignende på slutten av 1800-tallet ble foreslått av amerikaneren Frederick Taylor. I Russland ble dette gjort av vitenskapsmannen, revolusjonæren, filosofen og ideologen A. A. Bogdanov, som ga ut en bok om prinsippene for vitenskapelig ledelse i 1911. På grunnlag av bestemmelsene angitt i den, introduserte USSR NOT, det vil si den vitenskapelige organiseringen av arbeidskraft. Men det mest perfekte var 5C-systemet foreslått av den japanske ingeniøren Taiichi Ohno og introdusert av ham på Toyota Motor-anlegget i produksjon. Hva er det og hvorfor har det japanske systemet blitt så populært?
Faktum er at det er basert på et enkelt prinsipp som ikke krever kostnader. Den består iden neste - hver ansatt, fra renholder til direktør, bør optimalisere sin del i den generelle arbeidsflyten så mye som mulig. Dette fører til en økning i overskuddet av produksjonen som helhet og til en økning i inntekten til alle ansatte. Nå har stafettpinnen for innføringen av "5C"-systemet blitt plukket opp av bedrifter over hele verden, inkludert Russland. I denne artikkelen skal vi prøve å overbevise skeptikere om at japansk kunnskap virkelig fungerer, og i absolutt ethvert aktivitetsfelt.
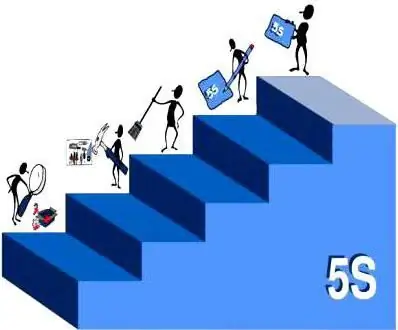
«5C»-systemet i produksjon, hva er det
International 5S står for fem trinn ("step" på engelsk step). Noen økonomer og pådrivere for en ny holdning til arbeid forklarer navnet med de fem japanske postulatene som er konsekvent implementert i 5S-systemet: seiri, seiton, seiso, seiketsu og shitsuke. For oss er våre innfødte "5Cs" nærmere og mer forståelige - fem påfølgende trinn som må fullføres for å oppnå velstanden til produksjonen vår. Dette er:
1. Sorter.
2. Holder orden.
3. Holder rent.
4. Standardisering.
5. Forbedring.
Som du kan se, krever ikke "5C"-systemet noe overnaturlig i produksjonen. Kanskje er det derfor man fortsatt kan møte mistillit og en useriøs holdning til henne.
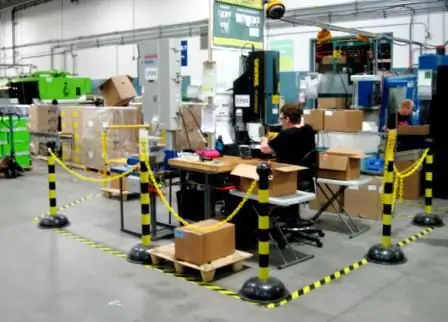
stadier for å lage et system
Den kloke japaneren Taiichi Ohno, som takket være introduksjonen av sine metoder på Toyota-fabrikken klarte å reise seg fraingeniør til administrerende direktør, la merke til hvor mange tap som oppstår på grunn av ulike inkonsekvenser og overlegg. For eksempel ble noen små skruer ikke satt på transportøren i tide, og som et resultat stoppet hele produksjonen. Eller omvendt, delene ble levert med margin, de viste seg å være overflødige, og som følge av dette måtte en av de ansatte ta dem med tilbake til lageret, noe som betyr å kaste bort tiden på tomt arbeid. Taiichi Ohno utviklet et konsept han k alte "just in time". Det vil si at nøyaktig så mange deler som trengs nå ble levert til transportøren.
Andre eksempler kan gis. "5S"-systemet i produksjon inkluderte også konseptet "kanban", som på japansk betyr "reklameskilt". Taiichi Ohno foreslo å feste en såk alt "kanban"-tag til hver del eller hvert verktøy, der all nødvendig informasjon om delen eller verktøyet ble gitt. I utgangspunktet gjelder det alt. For eksempel til varer, medisiner, mapper på kontoret. Det tredje konseptet som 5S-systemet i produksjon er basert på er konseptet «kaizen», som betyr kontinuerlig forbedring. Det ble også utviklet andre konsepter som kun var egnet for høyt spesialiserte produksjonsprosesser. I denne artikkelen vil vi ikke vurdere dem. Som et resultat av alle innovasjonene som er testet i praksis, har det blitt dannet 5 trinn som kan brukes for enhver produksjon. La oss analysere dem i detalj.
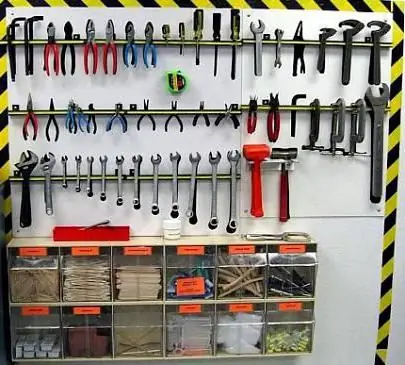
Sortering
Mange av oss har varer på stasjonære datamaskiner som, ii utgangspunktet ikke nødvendig. For eksempel gamle skjemaer, ubrukte filer, utkast til beregninger, en serviett som det var en kopp kaffe på. Og blant dette kaoset kan det være nødvendige filer eller dokumenter. De grunnleggende prinsippene til "5S"-systemet innebærer å optimere arbeidsflyten din, det vil si å sørge for at tiden ikke kastes bort på å lete etter de riktige tingene blant ruinene til det unødvendige. Dette er sortering. Det vil si at på arbeidsplassen (nær maskinen, på bordet, på verkstedet - hvor som helst), er alle gjenstander lagt ut i to hauger - det nødvendige og det unødvendige, som må avhendes. Videre er alt du trenger dekomponert i følgende hauger: "brukes ofte og konstant", "brukes sjelden", "nesten ikke brukt". Dette fullfører sorteringen.
Beholde orden
Hvis du bare demonterer varene, er det ingen mening. Det er nødvendig å ordne disse elementene (verktøy, dokumenter) i en slik rekkefølge at det som brukes konstant og ofte er i sikte, eller slik at det raskt kan tas og enkelt settes tilbake. Det som sjelden brukes kan sendes et sted i en boks, men det må festes en kanban-tag til slik at det etter en stund lett og nøyaktig kan finnes. Som du kan se, starter 5S-systemet på arbeidsplassen med de enkleste trinnene, men faktisk viser det seg å være veldig effektivt. Dessuten forbedrer det humøret og arbeidslysten.
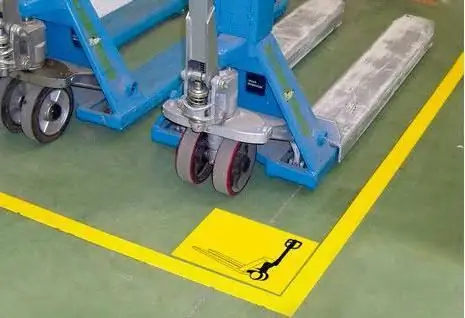
Keeping clean
Dette tredje trinnet er det mest logiske for mange. Vi har lært å være rene fra barndommen. Påi produksjon er det også nødvendig, og ikke bare bordene til kontorarbeidere eller skap i cateringbedrifter, men også maskiner, vaskerom til rengjøringsmidler skal være rene. I Japan tar ansatte godt vare på arbeidsplassene sine, de rengjøres tre ganger om dagen - om morgenen før jobb, ved lunsjtid og om kvelden, på slutten av arbeidsdagen. I tillegg har bedriftene deres innført spesiell merking av områder som lar dem observere orden i produksjonen, det vil si at områder med ferdige produkter, lagring av visse deler og så videre er merket med forskjellige farger.
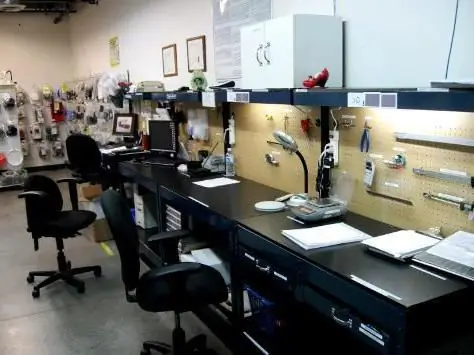
Standardisering
Prinsippene for standardisering ble oppfunnet av Taiichi Ohno. De er også mye brukt av det moderne 5S-systemet. Produksjonsstyring, takket være standardisering, får et fantastisk verktøy for å kontrollere alle prosesser. Som et resultat blir årsakene til forsinkelser fra tidsplanen raskt eliminert og feil som fører til utgivelse av lavkvalitetsprodukter blir rettet. På Toyota Motor-anlegget så standardiseringen slik ut: Formenn utarbeidet daglige arbeidsplaner, presise instrukser ble lagt ut på arbeidsplassen, og på slutten av arbeidsdagen sjekket spesialarbeidere hvilke avvik fra planen som skjedde i løpet av dagen og hvorfor. Dette er den grunnleggende regelen for standardisering, det vil si presise instruksjoner, arbeidsplaner og kontroll over implementeringen av dem. Nå innfører mange bedrifter, for eksempel ENSTO-anlegg i Estland, et bonussystem for ansatte som strengt overholder bestemmelsene i 5C-systemet og på grunnlag av dette øker produktiviteten, somer et stort insentiv til å ta i bruk dette systemet som en livsstil.
Forbedring
Det femte trinnet, som fullfører "5S"-systemet i produksjon, er basert på konseptet kaizen. Det betyr at alle ansatte, uansett stilling, bør strebe etter å forbedre arbeidsprosessen på det området de er betrodd dem. Den filosofiske essensen av kaizen er at hele livet vårt blir bedre for hver dag, og siden arbeid er en del av livet, bør det heller ikke holde seg unna forbedringer.
Aktivitetsfeltet her er bredt, for perfeksjon har ingen grenser. I følge japanernes konsepter skulle arbeiderne selv ønske å forbedre produksjonsprosessen sin, uten instruksjoner eller tvang. Nå bygger mange organisasjoner team med arbeidere som overvåker produktkvalitet, lærer andre om deres positive opplevelser og bidrar til å oppnå fortreffelighet.
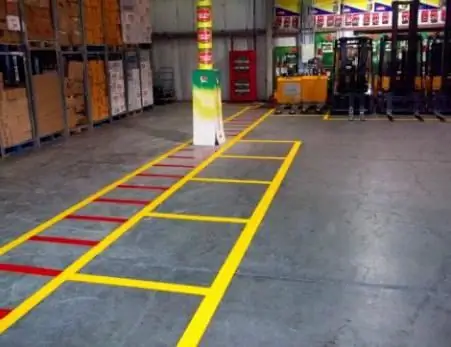
Grunnleggende feil
For at «5C»-systemet skal begynne å fungere, er det ikke nok å organisere det eller ansette ansatte som vil tvinge sine kolleger til å implementere det. Det er viktig at folk innser nytten av denne innovasjonen og aksepterer den som en livsstil. Innføringen av "5S"-systemet i Russland i produksjon står overfor vanskeligheter nettopp fordi vår russiske mentalitet er forskjellig fra den japanske. Mange av våre produksjoner er preget av følgende:
1. Ansatte, spesielt hvis det ikke er insentiver for dem, søker ikke å øke fortjenesten til bedriften. De spør,hvorfor prøve å gjøre sjefen enda rikere hvis han allerede har alt.
2. Lederne selv er ikke interessert i innføringen av «5S»-systemet, fordi de ikke ser hensiktsmessigheten i det.
3. Mange direktiver "ned fra oven" er vant til å utføre kun for "tick". I Japan er det en helt annen holdning til arbeidet deres. For eksempel tenkte den samme Taiichi Ohno, som introduserte "5S"-systemet, ikke på personlig vinning, men på fordelen med selskapet der han bare var ingeniør.
4. I mange virksomheter blir 5S-systemet tvangsintrodusert. Lean produksjon, som innebærer eliminering av tap av alle slag (arbeidstid, råvarer, gode ansatte, motivasjon og andre indikatorer), fungerer ikke, da arbeidere begynner å motstå innovasjoner på et underbevisst nivå, noe som til slutt reduserer all innsats til null.
5. Ledere som implementerer systemet forstår ikke helt essensen, noe som forårsaker feil i etablerte produksjonsprosesser.
6. Standardisering utvikler seg ofte til byråkrati, en god gjerning er overgrodd med instruksjoner og direktiver som kun forstyrrer arbeidet.
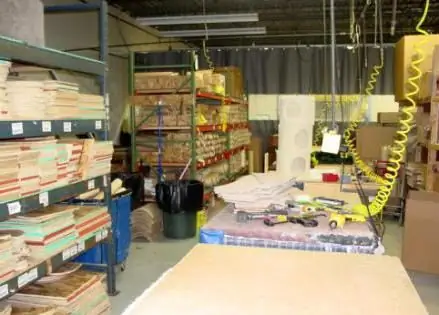
Anmeldelser
Russere som har introdusert "5S"-systemet i produksjon, tilbakemeldingene på denne innovasjonen er svært tvetydige. Uthevede fordeler:
- bedre å være på arbeidsplassen;
- ikke distrahere fra jobben med unødvendige småting;
- mer tydelig arbeidsflyt;
- trettheten avtok ved slutten av skiftet;
- litt øktlønn ved å øke arbeidsproduktiviteten;
- yrkesskader redusert.
Bemerkede ulemper:
- ved sortering tvinger de alt til å kastes;
- standardisering har ført til økt byråkrati;
- Introduksjonen av "5C"-systemet har ikke forverret problemene på alle områder av virksomheten;
- Å sette 5S-systemet på første plass har overskygget viktige problemer som mangelen på reservedeler.
Anbefalt:
Grunnleggende prinsipper for utlån: beskrivelse, funksjoner og krav
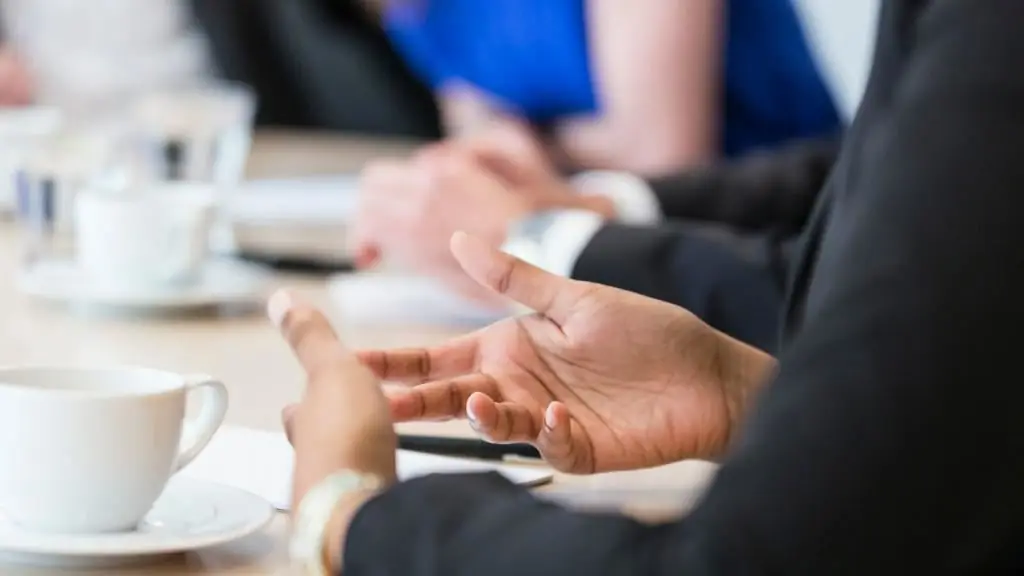
I vår vanskelige tid er folk ofte plaget av økonomiske problemer. En av de beste løsningene i denne situasjonen er et lån. Finn ut hva prinsippene for utlån er og om du oppfyller kriteriene for en eksemplarisk låntaker
Moderne produksjon. Strukturen til moderne produksjon. Problemer med moderne produksjon

Utviklet industri og et høyt nivå i landets økonomi er nøkkelfaktorer som påvirker rikdommen og velferden til befolkningen. En slik stat har store økonomiske muligheter og potensial. En betydelig del av økonomien i mange land er produksjonen
JSC "Yaroslavl Tire Plant": beskrivelse, produkter, produksjon og anmeldelser
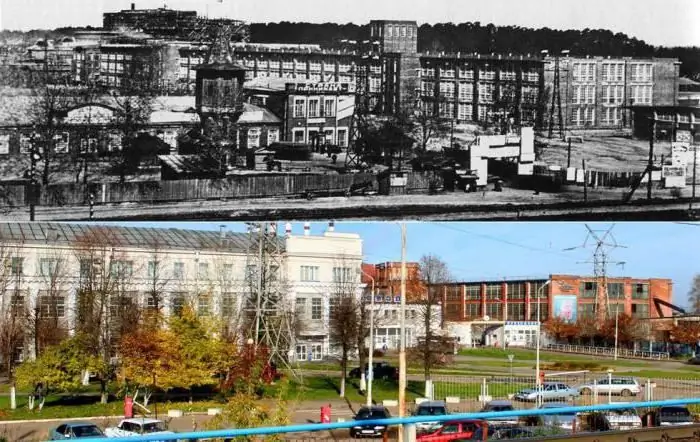
JSC Yaroslavl Tire Plant uten overdrivelse er lederen av landets dekkindustri. Hvert år produserer selskapet rundt 3 millioner enheter av høykvalitetsprodukter for ulike typer utstyr. Selskapet er en del av beholdningen "Cordiant"
Forretningsidé: produksjon av murstein. Teknologi og installasjon for produksjon av murstein
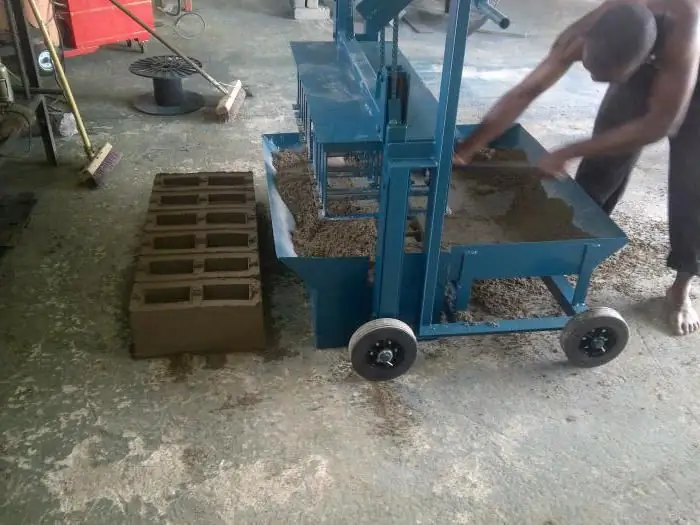
Du kan opprette din egen virksomhet som vil tilfredsstille dine behov og også bli en inntektskilde. Men for å oppnå høykvalitets murstein, er det nødvendig å overholde de tekniske forholdene og overholde produksjonsprosessen. Produksjonen av murstein hjemme innebærer ikke bruk av dyrt utstyr. Den viktigste betingelsen er riktig forberedelse av råvarer
Produksjon i garasjen: ideer fra Europa, foto. Produksjon av møbler, speil, nøkkelringer, souvenirmagneter, klokker i garasjen
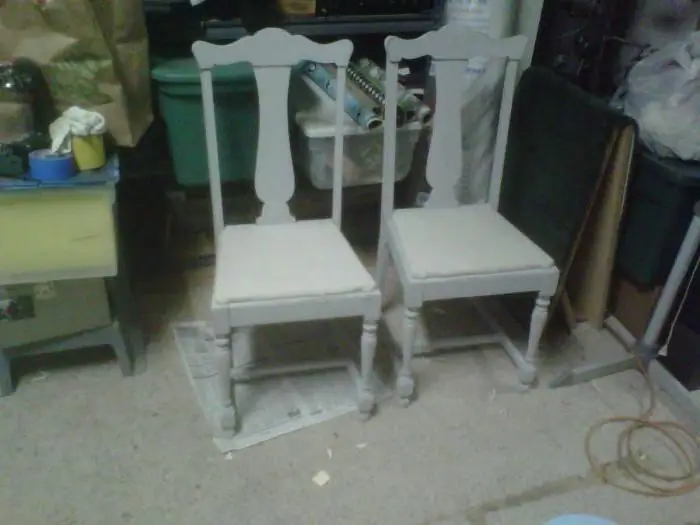
De fleste har tenkt på å starte egen bedrift minst én gang i livet. Hva kan en enkel mann i gata gjøre, spesielt hvis han ikke har mye kapital, men det er en ledig garasje?